1111111
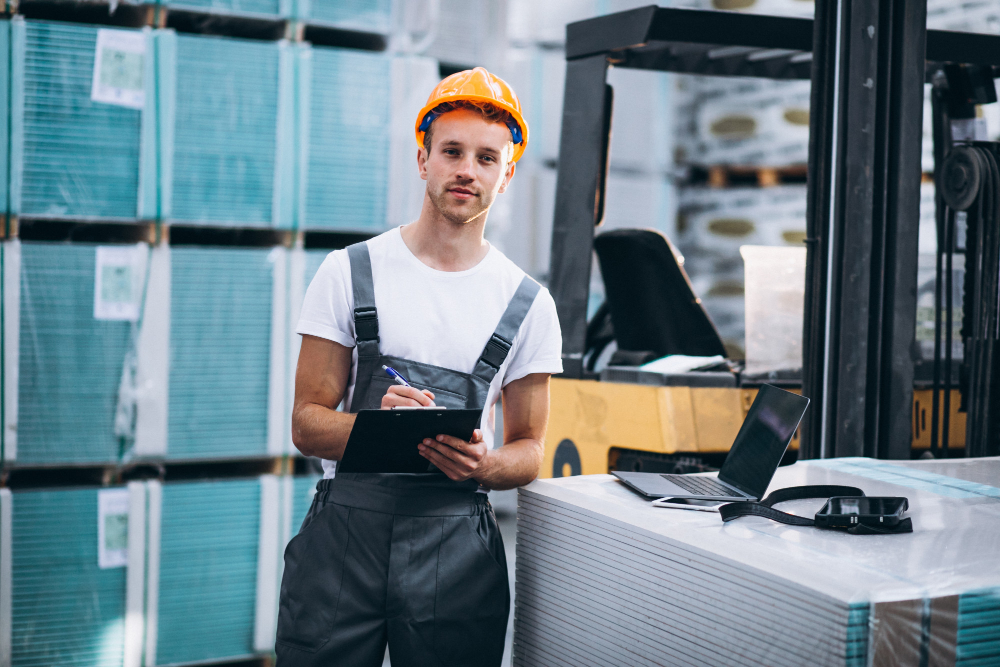
Kng
07/02/2025
0 Comments
Understanding Quality Control in Retail Fixture Manufacturing
Quality control in retail fixture manufacturing involves systematic processes designed to ensure products meet specified standards, creating durable, visually appealing, and functional fixtures for retail environments. It emphasizes precision and attention to detail at every stage of production.Key Aspects of Quality Control
- Material Inspection Materials like wood, metal, and glass undergo rigorous evaluation to ensure consistency, durability, and suitability for intended applications.
- Process Monitoring Manufacturing steps, such as cutting, welding, or assembly, are checked to ensure adherence to designs and specifications.
- Finished Product Testing Completed fixtures are tested for strength, stability, and aesthetic quality to meet customer expectations and industry standards.
The Key Role of Quality Control in Retail Environments
Quality control plays a pivotal role in ensuring that retail fixtures meet the demands of both functionality and aesthetics. Retail environments rely on durable, visually appealing fixtures to create a positive customer experience. An effective quality control process ensures that every product adheres to stringent standards, enhancing brand reputation and customer trust. Key aspects of quality control in retail environments include:- Material Inspection: Verifying raw materials for strength, safety, and compliance with industry standards.
- Durability Testing: Assessing the product’s ability to withstand wear and environmental conditions.
- Uniformity Checks: Ensuring design consistency across fixtures for cohesive branding.
- Functionality Reviews: Confirming operational features like mobility or modularity.
Crucial Standards and Regulations in Fixture Production
Adherence to industry standards and regulations is imperative in retail fixture production. Compliance ensures not only product quality but also safety and usability. Key benchmarks include:- Material Standards: Rules such as ASTM and ISO guide the selection of materials, ensuring durability and environmental sustainability.
- Safety Regulations: Fixtures must meet OSHA guidelines and local building codes to prevent accidents.
Top Challenges in Maintaining Quality Control
- Material Inconsistencies Variations in raw materials, such as wood, metal, or glass, pose a significant challenge to achieving uniformity in retail fixture production. Quality control teams must inspect and test materials rigorously to ensure compliance with specifications.
- Labor Skill Gaps Inconsistencies in craftsmanship often arise due to disparities in workforce expertise. Intensive training and clear standard operating procedures are critical to maintaining high manufacturing standards.
- Tight Production Timelines High demand and quick delivery expectations often pressure manufacturers to compromise on thorough quality checks. Striking a balance between efficiency and quality is crucial to meet client expectations.
- Equipment Malfunctions Outdated or poorly maintained machinery can lead to errors and defects. Regular maintenance schedules and advanced equipment monitoring systems are essential to minimize downtime and ensure precision.
- Regulatory Compliance Adhering to evolving safety and environmental regulations can complicate the production process. Dedicated teams must stay updated on these changes to avoid penalties and maintain product integrity.
Implementing Efficient Quality Control Processes
Efficient quality control processes are critical in retail fixture production to ensure consistent standards and minimize defects. Manufacturers can begin by integrating systematic inspections at key production stages, such as material selection, fabrication, assembly, and final finishing. Adopting advanced technologies like automated inspection systems or real-time monitoring tools helps identify irregularities promptly. Establishing clear benchmarks for durability, finish, and functionality ensures alignment with client specifications. Training employees on quality standards and reinforcing accountability fosters a culture of precision. Additionally, maintaining detailed quality reports promotes transparency and helps track trends over time, enabling continuous improvement efforts.Cutting-Edge Tools and Technologies for Quality Assurance
In retail fixture production, leveraging advanced tools and technologies ensures precision, efficiency, and reliability. Manufacturers now employ a variety of solutions designed to enhance quality assurance processes.- Automated Inspection Systems: These systems use high-resolution cameras and sensors to detect defects, ensuring every component meets strict standards.
- Computer-Aided Design (CAD) Software: CAD ensures accurate prototyping and enables digital simulations to identify potential issues before production begins.
- 3D Scanning and Printing: Integrated 3D technologies assist in rapid prototyping, enabling adjustments to be made efficiently.
- Digital Twin Technology: This innovation creates virtual replicas of fixtures for real-time analysis and troubleshooting.
The Role of Material Selection in Quality Control
Material selection serves as a cornerstone in achieving quality control within retail fixture production. The choice of materials directly affects the durability, functionality, and aesthetic appeal of fixtures, influencing product performance and customer satisfaction. Manufacturers must evaluate materials based on key factors such as:- Strength and Durability: Ensuring materials can withstand wear, load, and external factors.
- Cost-Effectiveness: Balancing quality with budget constraints.
- Aesthetic Value: Matching design standards and brand image.
- Sustainability: Aligning with environmental compliance and customer preferences.
Training and Development for Quality Control Teams
Effective training and development are critical for equipping quality control teams in retail fixture production with the necessary skills and expertise. A structured approach to training should include:- Technical Knowledge: Ensuring a thorough understanding of industry standards, material properties, and inspection techniques.
- Process Familiarity: Teaching standard operating procedures (SOPs) and quality metrics relevant to the production workflow.
- Problem-Solving Skills: Developing analytical abilities to identify root causes and implement corrective actions effectively.
- Technology Training: Familiarizing staff with advanced inspection tools, software, and automation technologies.
The Impact of Quality Control on Brand Reputation and Customer Experience
Effective quality control in retail fixture production significantly influences brand reputation and customer experience. Customers associate high-quality fixtures with professionalism and reliability, creating a positive perception of the brand. Poorly crafted fixtures, on the other hand, can tarnish trust and deter potential clients.Key Impacts of Quality Control:
- Enhanced Reliability: Retailers depend on fixtures for durability and functionality, which builds confidence in the brand.
- Customer Satisfaction: Superior fixtures contribute to seamless in-store experiences, leaving customers impressed.
- Brand Differentiation: Outstanding quality sets the brand apart in a competitive market.
Strategies for Continuous Improvement in Fixture Quality Management
To ensure consistent excellence in retail fixture production, implementing strategies that drive ongoing improvement is vital. Key approaches include:- Regular Quality Audits: Conduct routine inspections to identify defects and track compliance with quality standards. Audits help maintain transparency and pinpoint areas for enhancement.
- Data-Driven Insights: Leverage analytics tools to monitor production metrics, detect inefficiencies, and predict potential issues before they arise.
- Supplier Collaboration: Foster partnerships with material vendors to establish shared quality benchmarks and ensure consistent component reliability.
- Employee Training Programs: Continuously upskill teams on emerging technologies, materials, and quality control techniques to enhance precision and craftsmanship.